アイディアをバリューに
クリエイティブをグローバルに
1950年、日本で初めて冷間圧造の加工機(フォーマー)を導入して以来、 蓄積された研究開発技術とエンジニアのノウハウを活かし、 高品質・低コスト・短納期でお客様のニーズにお応えします。 先端技術と培った技術の融合による、「人」と「ものづくり」の繋がりで、創造性を大切にしています。
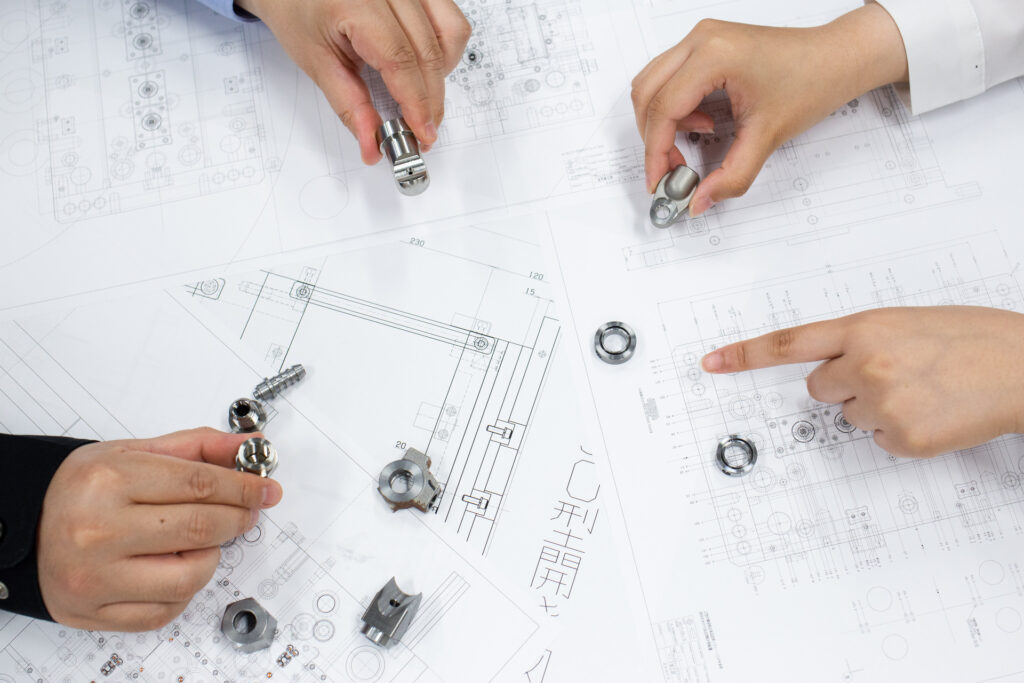
1950年、日本で初めて冷間圧造の加工機(フォーマー)を導入して以来、 蓄積された研究開発技術とエンジニアのノウハウを活かし、 高品質・低コスト・短納期でお客様のニーズにお応えします。 先端技術と培った技術の融合による、「人」と「ものづくり」の繋がりで、創造性を大切にしています。
圧造加工は、加工温度の違いで3つの種類に分けられます。
加工する金属の材質や生産量、最終製品の形状に応じて、最適な加工方法をご提案いたします。
冷間圧造とは、塑性加工の原理による、金属加工方法の1つです。
「塑性」とは金属の性質の1つで、ある一定の力を加えて変形させると「元に戻らない」性質のことです。この性質を持つ素材として「炭素鋼」があり、塑性加工とはその性質を利用し、金属などを希望の形状に変形させることです。
そして冷間圧造加工は、この塑性加工方法の1つで、コイル状の素材を必要な長さに切断したあと、熱を加えることなく「ヘッダー・ホーマー」と呼ばれる冷間圧造機で成形する加工方法です。
コイル状の材料を常温で連続的に切断し、切断されたブランクを搬送しながら多段(4〜6段)で成型します。
素材をそのまま加工するため、切削加工と違い材料ロスも少ない上に、加工スピードも早く、熱による歪みも少ないのが特徴です。
また、加工精度が高く、均一な製品を作ることができます。
PR:当社では、中国に自社金型工場を所有し、日本、中国間で連携した工程設計・金型設計により金型を内製で行うことにより、製品の制度・品質・コスト面で顧客のニーズにお応えしています。
特殊配管継手:80万本/月産
自動車用配光調整ネジ:150万本/月産
転造とは、冷間圧造と同じく、塑性加工の工法の1つです。
強い力を加えて素材を変形させる加工で、「転造」という名前のとおり、転造ダイスと呼ばれる金型の間に棒状の加工素材を回転させながら成形する方法です。 この転造は、主に「おねじ」の成形用に利用されている加工方法で、汎用ねじの大量生産に多く使用されています。
転造は少量生産には向きませんが、加工時間を大幅に短縮でき、生産性も大幅アップします。大量生産が可能となるため、ねじの製品単価を抑えられるというメリットがあります。
また、切削加工と異なり、加工中に削りくずを出さないため材料にムダがありません。コストを下げるとともに、環境に優しい加工法と言うこともできるでしょう。
PR:当社では、複合転造が主流となっております。切削で加工していた製品溝を転造で加工し量産化に成功をはじめ、製品用途・機能による形状のご提案が可能です。
自動車用配光調整ネジ:120万本/月
自動車用ランブ固定ピン、ネジ:60万本/月
精密部品の複合切削加工とは、当社で切削している自動車向け部品は、異なる軸上に設定された各部位の位置精度や寸法精度、表面粗さなどが厳しく設定されている一般的な金属加工部品などに比べて加工が困難な精密部品を多く取り扱っております。
これら精密部品を量産加工する為には、旋盤加工とフライス加工を同一工程で行える複合加工機能と斜め穴や多面加工が可能な付加1軸機能、又、それら機能を使いこなす技術力が必要となります。
当社では上記機能を有した自動盤を使用して複雑な部品の生産を行っております。
PR:当社は、本加工の出来る自動盤を海外工場含め合計100台以上を保有し、これら設備で量産中の製品は大小合わせ月間150万本の大量生産を実現しております。
また、軟鋼から高炭素鋼・合金鋼・ステンレスと多様な材質の加工実績があります。国内本社工場の加工技術は海外工場にも随時展開しており、海外においても日本と同水準の品質を維持・確保しております。
射出成形とは、プラスチック材料を加熱した筒内(シリンダー)で溶かし、その溶かした材料をシリンダー内のスクリュー等を用いて金型内に射出、金型内で冷却し、固化させる事で任意の形状に加工する工法。
当社では、射出成形以外にもガスアシスト成形、竪型成形機によるインサート成形(海外拠点含む)も行っております。
ガスアシスト成形とは、樹脂の射出後、高圧の不活性ガスを注入し製品内部より圧力を掛け、内部に空洞(中空部)を形成する成形方法。
PR:当社ではガスアシスト成形では難しかった形状品、多数個取り化のご提案が可能です。
50%のガラス繊維が含有されたポリアミド樹脂はガスインジェクションにとって偏肉しやすい樹脂ですが、量産化に成功しました。
調整ネジ:00本
ソレノイドとは、銅線をらせん状に巻線したコイルの中に棒状の鉄心を組込み、コイルに電流を流すことで磁界を発生させ、この棒状鉄心を磁力で吸引し直進運動させる部品です。
弊社ソレノイドの特徴
自動車向けシートベルト、シフトロック、ヘッドランプ用ソレノイドを生産(さらに用途拡大を推進中)
2. コスト低減
自社中国工場で生産
当社が得意とする切削・圧造・樹脂成形技術を用いて大半の部品を自社で製造可能
3. 品質重視
通常の組立工程内の定期品質チェックだけではなく、常にFMEAを評価し、未然防止活動を進め、作動耐久・連続通電耐久・冷熱サイクル試験等の重要試験を定期的に実施。
PR:ソレノイド:50万個
弊社のサービス内容や、製品について
ご相談・ご質問等ございましたら、お気軽にお問い合わせください。
弊社のサービス内容や、製品について
ご相談・ご質問等ございましたら、
お気軽にお問い合わせください。
お電話/FAXでのお問い合わせ
TEL.055-925-2000 / FAX.055-925-2005